Abstract
Underwater robots play a critical role in marine exploration, industrial inspection, and scientific research. However, drag forces in aquatic environments significantly affect their mobility, energy efficiency, and operational performance. This paper presents a comprehensive review of research advancements in drag reduction design for underwater robots, focusing on three primary directions: shape optimization, surface material innovation, and system-level functional design. Through a detailed analysis of literature and experimental studies, the underlying mechanisms, key technologies, and application cases of each drag reduction strategy are discussed. Additionally, research methodologies such as biomimicry, computational fluid dynamics (CFD), and modular design are evaluated. The paper concludes with insights into current challenges and future trends, emphasizing the integration of multidisciplinary approaches to enhance the hydrodynamic performance of underwater robots.
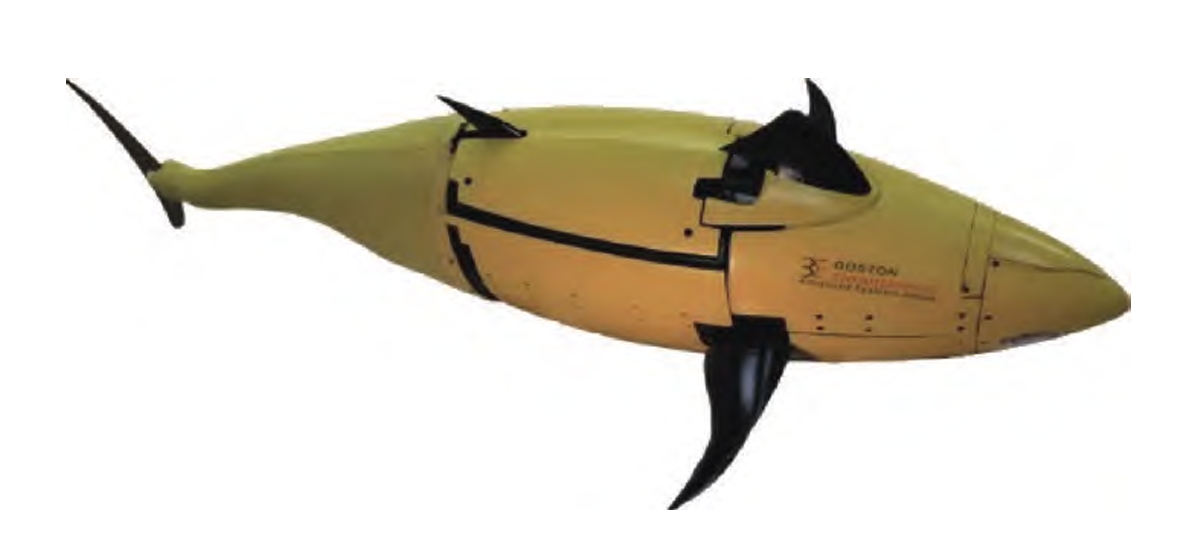
Keywords: underwater robot; drag reduction; biomimicry; surface materials; hydrodynamic design; system optimization
1. Introduction
Underwater robots, including manned submersibles and unmanned underwater vehicles (UUVs), are indispensable for navigating complex marine environments. However, the hydrodynamic drag they encounter imposes significant limitations on speed, energy consumption, and task efficiency. Drag in water is primarily composed of viscous drag (friction) and non-viscous drag (pressure differences), with viscous drag accounting for 70–80% of total drag in streamlined bodies . Reducing these forces is critical for extending operational range, improving maneuverability, and enhancing energy efficiency.
This review synthesizes research from Chinese National Knowledge Infrastructure (CNKI) and Web of Science databases, focusing on publications between 2000 and 2022. Key findings reveal three dominant research clusters: shape-based drag reduction, surface material innovation, and system-level functional optimization. Each area is discussed in detail, supported by experimental data and case studies.
2. Drag Reduction Through Shape Optimization
The external geometry of an underwater robot directly influences both frictional and pressure drag. Shape optimization strategies can be categorized into three main types: streamlined, frame-based, and hybrid designs, each with distinct hydrodynamic characteristics and application scenarios.
2.1 Streamlined Designs
Streamlined shapes, characterized by smooth, teardrop-like profiles, minimize turbulence and pressure differences. These designs are widely used in autonomous underwater vehicles (AUVs) and biomimetic robots.
2.1.1 Subtypes of Streamlined Shapes
- Torpedo-shaped: This design features an elliptical head and tapered tail, reducing both pressure and frictional drag. Examples include the Afalina-1 vehicle by the Leningrad Ordnance Institute, which incorporates a torpedo shape with biomimetic tail fins to minimize resistance . The “Qianlong-1” AUV developed by the Chinese Academy of Sciences uses a similar profile to reduce turbulence at depths up to 6,000 meters .
- 梭形 (Spindle-shaped): Inspired by tuna, this design tapers at both ends to minimize frontal area. The GhostSwimmer robot, modeled after bluefin tuna, achieves significant drag reduction, with its upgraded version, BIOSwimmer, maintaining a spindle shape while integrating propellers for enhanced mobility .
- 碟形 (Disk-shaped): Disk-shaped robots like Discuz and BOOMERANG leverage pressure differences between the center and edges to generate lift, reducing drag. CFD simulations confirm that disk-shaped designs can achieve lower resistance at high speeds compared to traditional hulls .
2.1.2 Performance Comparison
Table 1 summarizes the hydrodynamic performance of different streamlined subtypes:
Shape Type | Pressure Drag Reduction | Frictional Drag Reduction | Maneuverability | Application Examples |
---|---|---|---|---|
Torpedo-shaped | High (20–30% reduction) | Moderate (10–15% reduction) | High | Afalina-1, Qianlong-1 |
Spindle-shaped | Very high (30–40% reduction) | Low (5–8% reduction) | Moderate | GhostSwimmer, Tunabot |
Disk-shaped | Moderate (15–20% reduction) | High (15–20% reduction) | Low | Discuz, BOOMERANG |
Table 1. Performance comparison of streamlined underwater robot designs.
2.2 Frame-Based Designs
Frame-based underwater robots feature open truss structures, offering modularity and payload flexibility but compromising hydrodynamic efficiency. The large frontal area and protruding components increase both frictional and pressure drag. For example, pipeline inspection robots with add-on manipulators exhibit 15–20% higher drag than streamlined models . While frame designs are suitable for stable, low-speed environments, their high drag limits applications requiring rapid movement.
2.3 Hybrid Designs
Hybrid designs combine streamlined bodies with modular frames to balance drag reduction and functionality. The SAUVIM vehicle, for instance, integrates a streamlined upper hull for low resistance and a frame-based lower section for attaching manipulators . Amphibious robots like the dual 髻鲨 (hammerhead shark)-inspired design reduce drag by 23% through a streamlined canopy and tracked frame . Table 2 compares the key characteristics of shape-based designs:
Design Type | Drag Reduction Mechanism | Advantages | Limitations |
---|---|---|---|
Streamlined | Smooth profile reduces turbulence | High efficiency, simple fabrication | Limited payload space |
Frame-based | Modular structure for attachments | High functionality | High drag, poor maneuverability |
Hybrid | Combined streamlined and frame | Balanced efficiency and flexibility | Complex design |
Table 2. Overview of shape-based drag reduction strategies.
3. Surface Material Innovations for Drag Reduction
Surface materials significantly influence frictional drag by altering fluid-solid interactions. Research in this area focuses on biomimetic materials inspired by marine organisms, categorized into rigid, flexible, and hybrid structures.
3.1 Rigid Biomimetic Materials
Rigid materials mimic the non-smooth surfaces of sharks, where dermal denticles reduce turbulence. These structures are typically simplified into triangular or rectangular ribs for practical fabrication. For example, a thin ribbed 贴面 (贴面) inspired by shark skin reduced hull drag by 6–8% in 水槽试验 (flume tests) . CFD studies show that rigid microstructures stabilize boundary layers, delaying transition to turbulent flow .
3.2 Flexible Materials
Flexible materials, emulating dolphin skin, reduce drag by absorbing flow energy and delaying laminar-turbulent transition. Dolphin-inspired polyurethane elastomers with dermal ridge structures achieved drag reduction rates of over 10% at speeds above 10 m/s . Whale skin-inspired thermal boundary layer control, using black-and-white coloration to induce heat transfer, reduced friction by 7% in 平板试验 (flat plate tests) .
3.3 Hybrid (Rigid-Flexible) Materials
Hybrid materials combine rigid and flexible features, such as the pufferfish’s spines and mucus. 仿生河鲀表皮 (pufferfish-inspired surfaces) with rigid spines and 柔性黏液层 (flexible mucus layers) demonstrated superior drag reduction compared to single-material designs, with experiments showing a 15% reduction in turbulent drag . Table 3 summarizes key material-based strategies:
Material Type | Biomimetic Model | Key Mechanism | Drag Reduction Rate |
---|---|---|---|
Rigid | Shark skin | Micro-riblets stabilize boundary layers | 6–10% |
Flexible | Dolphin skin | Elastic deformation absorbs flow energy | 10–15% |
Hybrid | Pufferfish | Combined rigid spines and mucus | 15–20% |
Table 3. Surface material strategies for drag reduction.
4. System-Level Functional Drag Reduction
System-level designs optimize internal layouts and propulsion methods to minimize drag. This involves both structural optimization and innovative actuation technologies.
4.1 Layout Optimization
Efficient component placement reduces frontal area and turbulence. Genetic algorithms have been used to optimize topological structures, achieving 8–12% drag reduction by minimizing protrusions and streamlining airflow . Key principles include placing attachments away from the head and reducing their size, as demonstrated in CFD-based optimization studies .
4.2 Innovative Propulsion Systems
Biomimetic propulsion, such as body/caudal fin (BCF) and median/paired fin (MPF) modes, offers lower drag and noise compared to traditional propellers. Table 4 lists representative BCF and MPF prototypes:
Research Institution | Year | Biomimetic Model | Propulsion Mode | Drag Reduction | Key Feature |
---|---|---|---|---|---|
MIT Robotuna | 1994 | Bluefin tuna | BCF | 15% | 91% propulsion efficiency |
中国科学技术大学 (USTC) | 2008 | Blue-spotted ray | MPF | 10% | Flexible undulating fin |
德国 Festo | 2018 | Cuttlefish | MPF | 12% | 3D-printed seamless fin |
Table 4. Biomimetic propulsion systems in underwater robots.
Other innovations include artificial muscle-driven fish and jellyfish-inspired robots. The “Cyro” jellyfish robot, using rubber bell contractions, reduces energy consumption by 20% during ascent .
5. Research Methodologies
5.1 Biomimetic Design
Biomimicry involves replicating natural structures, such as shark denticles or dolphin skin, through 3D printing or coating technologies. For example, a boxfish-inspired pressure hull reduced drag by 18% while improving stability .
5.2 Computational Fluid Dynamics (CFD)
CFD simulations are widely used to optimize shapes and materials. Coupled with genetic algorithms, CFD has achieved multi-objective optimization, reducing drag by up to 12.07% in model studies .
5.3 Experimental Testing
Wind tunnels and water flumes validate theoretical models. For instance, drag reduction of superhydrophobic coatings was tested in turbulent flows, showing a 30% resistance decrease at high Reynolds numbers .
6. Challenges and Future Directions
6.1 Current Challenges
- Multi-objective optimization: Balancing drag reduction with payload capacity and structural strength remains difficult.
- Material durability: Biomimetic surfaces often degrade in harsh marine environments, limiting practical application.
- Energy efficiency: While biomimetic propulsion is efficient, energy storage and actuation technologies lag behind design demands.
6.2 Future Trends
- Integrated biomimicry: Combining shape, material, and propulsion 仿生 (e.g., fully biomorphic robots) to achieve synergistic drag reduction.
- Smart materials: Developing self-adaptive surfaces (e.g., temperature-responsive coatings) for dynamic drag control.
- AI-driven design: Using machine learning to optimize complex, multi-variable systems in real time.
7. Conclusion
Drag reduction is a critical frontier in underwater robot design, with advancements in shape optimization, surface materials, and system-level engineering offering significant performance gains. By leveraging biomimicry, computational tools, and interdisciplinary innovation, researchers can develop more efficient, agile, and durable underwater robots. Future breakthroughs will likely emerge from integrating AI, smart materials, and advanced manufacturing techniques, paving the way for next-generation marine exploration and industrial applications.